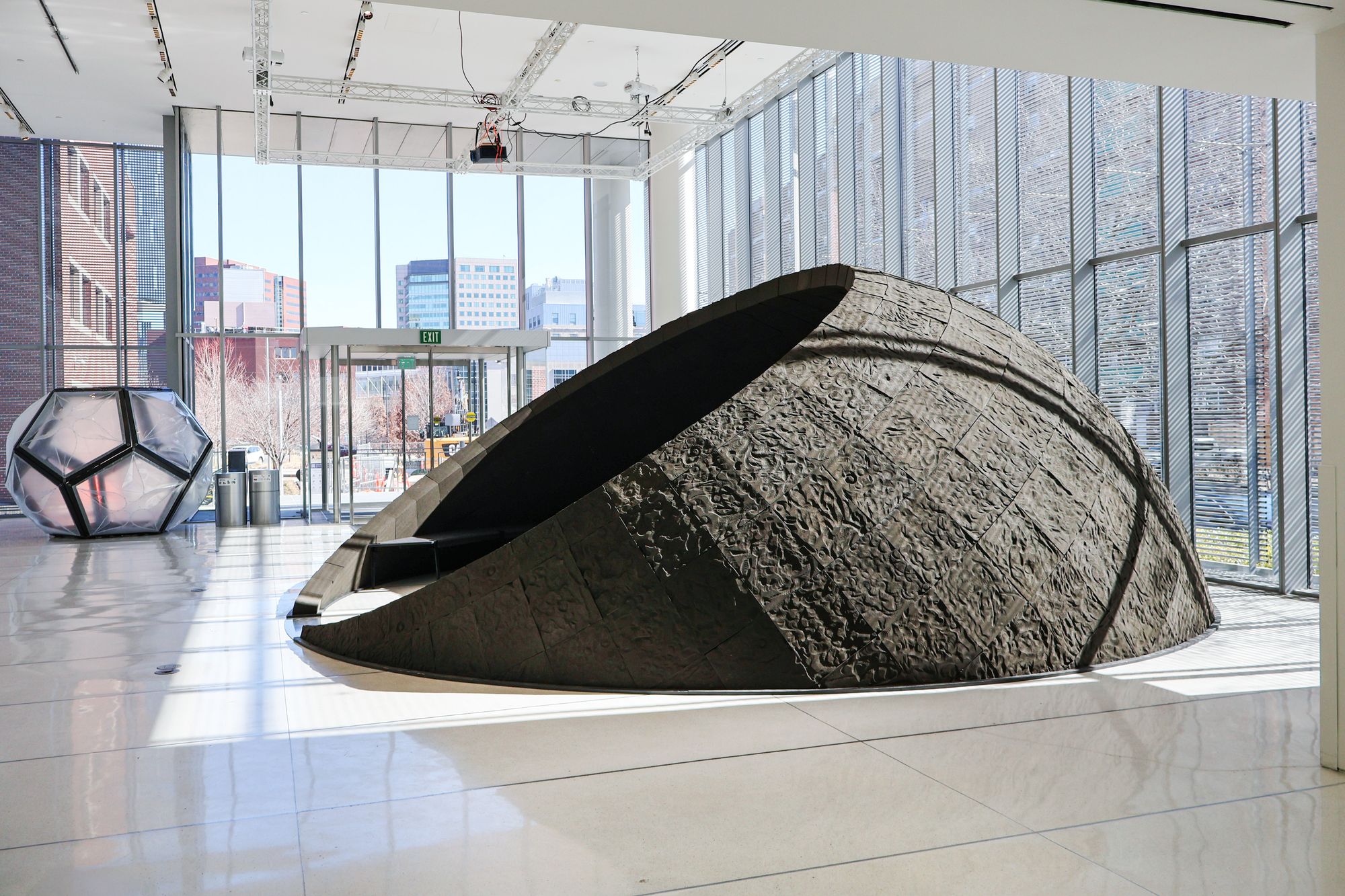
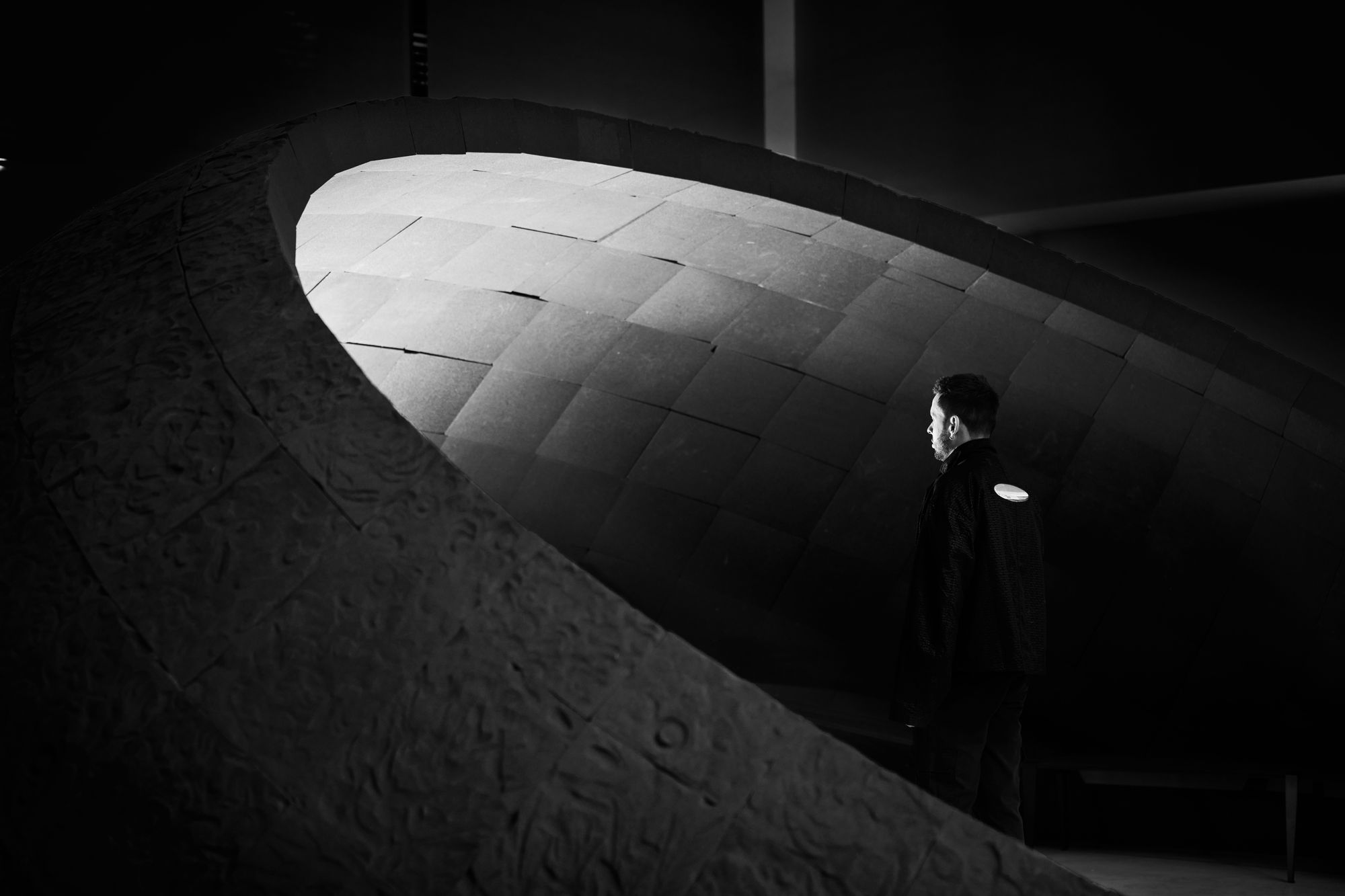
MIT students and faculty designed and fabricated a control room for a unique lunar landing mission. Built from lightweight cellular glass, the compression structure is a conceptual and technical achievement made possible through multidisciplinary collaboration.
By Adelaide Zollinger
Apr 2, 2025
On March 6, in one of the first U.S. lunar landings since the Apollo era, MIT sent three payloads — the AstroAnt, the RESOURCE 3D camera, and the HUMANS nanowafer — to the moon’s south polar region. The MIT component of the mission was based out of Luna, a control space designed by MIT Department of Architecture students and faculty in collaboration with the MIT Space Exploration Initiative, Inploration, and Simpson Gumpertz and Heger. Luna is installed in the MIT Media Lab ground-floor gallery and opened to the public as part of Artfinity, MIT’s Festival for the Arts. The installation allows visitors to observe payload operators at work and interact with the software used for the mission, thanks to virtual reality.
Video by Jabari Canada, MIT M.Arch Candidate '26; courtesy of MIT Architecture and MIT Media Lab.
While the lunar mission ended prematurely, the team says it achieved success in the design and construction of a control room embodying MIT’s design approach and capacity to explore new technologies while maintaining simplicity.
A central hub for mission operations, the control room is a structural and conceptual achievement, balancing technical challenges with a vision for an immersive experience, and the result of a multidisciplinary approach. “This will be our Moon on Earth,” says Mateo Fernandez, a third-year MArch student and 2024 MAD Design Fellow, who designed and fabricated Luna in collaboration with Nebyu Haile, a PhD student in the Building Technology Program in Architecture, and Simon Lesina Debiasi, a research assistant in the SMArchS Computation program and part of the Self-Assembly Lab. “The design was meant for people — for the researchers to be able to see what's happening at all times, and for the spectators to have a 360 panoramic view of everything that's going on,” explains Fernandez. “A key vision of the team was to create a control room that broke away from the traditional, closed-off model — one that instead invited the public to observe, ask questions, and engage with the mission,” adds Haile.
For this project, students were advised by Skylar Tibbits, founder and co-director of the Self-Assembly Lab, associate professor of design research, and MAD’s assistant director for education; J. Roc Jih, associate professor of the practice in architectural design; John Ochsendorf, MIT Class of 1942 Professor with appointments in the departments of Architecture and Civil and Environmental Engineering, and founding director of MAD; and Brandon Clifford, associate professor of architecture. The team worked closely with Cody Paige, director of the Space Exploration Initiative at the Media Lab, and her collaborators, emphasizing that they “tried to keep things very minimal, very simple, because at the end of the day,” explains Fernandez,
we wanted to create a design that allows the researchers to shine and the mission to shine.
“This project grew out of the Space Architecture class we co-taught with Cody Paige and astronaut and MIT AeroAstro faculty member, Jeff Hoffman” in the fall semester, explains Tibbits. “Mateo was part of that studio, and from there, Cody invited us to design the mission control project. We then brought Mateo onboard, Simon, Nebyu, and the rest of the project team.” According to Tibbits,
this project represents MIT’s mind-and-hand ethos. We had designers, architects, artists, computational experts, and engineers working together, reflecting the polymath vision — left brain, right brain, the creative and the technical coming together to make this possible.
Luna was funded and informed by Tibbits and Jih’s Professor Amar G. Bose Research Grant Program. “J. Jih and I had been doing research for the Bose grant around basalt and mono-material construction,” says Tibbits, adding that they “had explored foamed glass materials similar to pumice or foamed basalt, which are also similar to lunar regolith.” “FOAMGLAS® is typically used for insulation, but it has diverse applications, including direct ground contact and exterior walls, with strong acoustic and thermal properties,” says Jih. “We helped Mateo understand how the material is used in architecture today and how it could be applied in this project, aligning with our work on new material palettes and mono-material construction techniques.”
Additional funding came from Inploration, a project run by creative director, author, and curator Lawrence Azerrad, as well as expeditionary artist, curator, and analog astronaut artist Richelle Ellis, and Comcast, a Media Lab member company. It was also supported by the MIT Morningside Academy for Design (MAD) through Fernandez’s Design Fellowship. Additional support came from industry members such as Owens Corning (construction materials), Bose (communications), as well as MIT Media Lab member companies, Dell Technologies (operations hardware), and Steelcase (operations seating).
Luna looks like variations of the Moon, offering different perspectives of the Moon’s round or crescent shape depending on the viewer’s position.
What’s remarkable is how close the final output is to Mateo’s original sketches and renderings,” Tibbits notes. “That often doesn’t happen — where the final built project aligns so precisely with the initial design intent.
Luna’s entire structure is built from FOAMGLAS®, a durable material composed of glass cells usually used for insulation. “FOAMGLAS® is an interesting material,” says Lesina Debiasi, who supported fabrication efforts, ensuring a fast and safe process. “It’s relatively durable and light but can easily be crumbled with a sharp edge or blade, requiring every step of the fabrication process — cutting, texturing, sealing — to be carefully controlled.”
Fernandez, whose design experience was influenced by the idea that “simple moves” are most powerful, explains: “We’re giving a second life to materials that are not thought of for building construction… and I think that's an effective idea. Here, you don't need wood, concrete, rebar — you can build with one material only.” While the interior of the dome-shaped construction is smooth, the exterior was hand textured to evoke the basalt-like surface of the Moon.
The light-weight cellular glass produced by Owens Corning, who sponsored part of the material, comes as an unexpected choice for a compression structure — a type of architectural design where stability is achieved through the natural force of compression, usually implying heavy materials. The control room doesn’t use connections or additional supports, and depends upon the precise placement, size and weight of individual blocks to create a stable form from a succession of arches.
Traditional compression structures rely on their own weight for stability, but using a material that is more than ten times lighter than masonry meant we had to rethink everything. It was about finding the perfect balance between design vision and structural integrity,
reflects Haile, who was responsible for the structural calculations for the dome and its support.
Compression relies on gravity and wouldn’t be a viable construction method on the Moon itself. “We’re building using physics, loads, structures, and equilibrium to create this thing that looks like the Moon, but depends on Earth’s forces to be built. I think people don't see that at first, but there’s something cheeky and ironic about it,” confides Fernandez, acknowledging that the project merges historical building methods with contemporary design.
The location and purpose of Luna — both a work space and an installation engaging the public — implied balancing privacy and transparency to achieve functionality. “One of the most important design elements that reflected this vision was the openness of the dome,” says Haile.
We worked closely from the start to find the right balance — adjusting the angle and size of the opening to make the space feel welcoming while still offering some privacy to those working inside.
With the FOAMGLAS® material, the team had to invent a fabrication process that would achieve the initial vision while maintaining structural integrity. Sourcing a material with radically different properties compared to conventional construction implied collaborating closely on the engineering front, the lightweight nature of the cellular glass requiring creative problem-solving: “what appears perfect in digital models doesn’t always translate seamlessly into the real world,” shares Haile, “The slope, curves, and overall geometry directly determine whether the dome will stand, requiring Mateo and me to work in sync from the very beginning through the end of construction.” While the engineering was primarily led by Haile and Ochsendorf, the structural design was officially reviewed and approved by Paul Kassabian at Simpson Gumpertz & Heger (SGH), ensuring compliance with engineering standards and building codes.
“None of us had worked with FOAMGLAS® before, and we needed to figure out how best to cut, texture, and seal it,” says Lesina Debiasi.
Since each row consists of a distinct block shape and specific angles, ensuring accuracy and repeatability across all the blocks became a major challenge. Since we had to cut each individual block four times before we were able to grove and texture the surface, creating a safe production process and mitigating the distribution of dust was critical,
he explains. “Working inside a tent, wearing personal protective equipment like masks, visors, suits, and gloves made it possible to work for an extended period with this material.”
In addition, manufacturing introduced small margins of error threatening the structural integrity of the dome, prompting hands-on experimentation. “The control room is built from 12 arches,” explains Fernandez. “When one of the arches closes, it becomes stable, and you can move on to the next one… Going from side to side, you meet at the middle and close the arch using a special block — a keystone, which was cut to measure,” he says. “In conversations with our advisors, we decided to account for irregularities in the final keystone of each row. Once this custom keystone sat in place, the forces would stabilize the arch and make it secure,” adds Lesina Debiasi.
This project exemplified the best practices of engineers and architects working closely together from design inception to completion — something that was historically common but is less typical today,” says Haile. “This collaboration was not just necessary — it ultimately improved the final result.
Fernandez, who is supported this year by the MAD Design Fellowship, expressed how “the fellowship gave [him] the freedom to explore [his] passions and also keep [his] agency.”
“In a way, this project embodies what design education at MIT should be,” Tibbits reflects. “We’re building at full scale, with real-world constraints, experimenting at the limits of what we know — design, computation, engineering, and science. It’s hands-on, highly experimental, and deeply collaborative, which is exactly what we dream of for MAD and MIT’s design education more broadly.”
Luna, our physical lunar mission control highlights the incredible collaboration across the Media Lab, Architecture, and the School of Engineering to bring our lunar mission to the world. We are democratizing access to space for all!
MIT
DESIGN LEAD
Mateo Fernandez, MIT Architecture, MArch student; MIT MAD (Morningside Academy for Design), 2024 Design Fellow
STRUCTURAL LEAD
Nebyu Haile, MIT Architecture, Building Technology Program, PhD
FABRICATION LEAD
Simon Lesina Debiasi, MIT Architecture, SMArchS Computation program; Self-Assembly Lab, research assistant
PROJECT
Nof Nathansohn, Farida Moustafa, Arzy Abliadzhyieva, Nebyu Haile, Oliver Moldow, Jared Laucks
FACULTY
External partners & funding
Jul 4, 2024
Oct 4, 2024
May 14, 2024